High-performance aluminum circular saw, fully automatic VA-L350NC2 with servo-motor feed
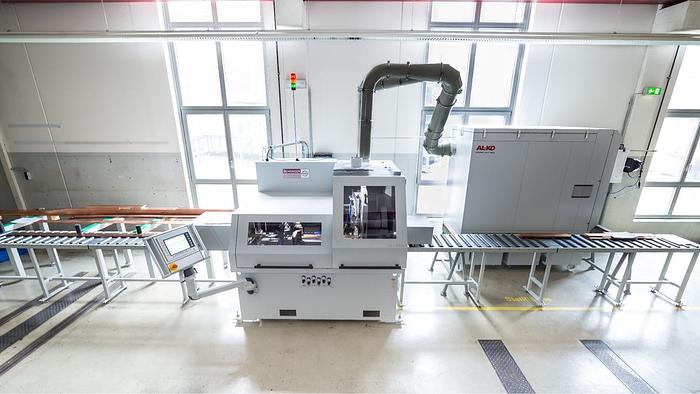
High-performance aluminum circular saw, fully automatic VA-L350NC2 with servo-motor feed
Location:Sankt Leon-Rot, Germany
Description
The machine consists of a robust sawing machine base with an integrated clamping/replenishment device and the saw unit for the economical processing of aluminum profiles and solid aluminum material for 90° cuts.
The VA-L350NC2 is designed for use with carbide-tipped circular saw blades with a diameter of 400mm.
When open, the generously dimensioned protective hoods enable optimal access to the entire inner machine area. The machine is covered with insulating protection material.
Cutting range (only 90° cuts)
maximum with a saw blade diameter of 400mm:
· Around 10-115mm
Rectangle 10 x 10-200 x 70mm
· Square 10-100mm
Saw Unit
Frequency-controlled drive, power 15kW, the speed is adjustable in the range of 800-4200 rpm.
The saw blade feed on the rocker is servo-motorized to reduce non-productive times and is adjustable in the range of 1-500mm/s. The return stroke can be performed with a maximum acceleration of up to 2g (20,000mm/s2). Start and stop positions are freely programmable.
Saw blade cooling/lubrication
The machine is equipped with a micro-spray device for micro-fine spraying of the carbide saw blades with double level monitoring and a tank capacity of
3 liters designed. The friction between the saw blade and the material is reduced and the saw blade is cooled at the same time, which improves the cut surface and increases the service life.
The level monitoring included as standard issues a warning message on the control panel if there is still a residual amount of cooling lubricant in the tank. However, you can continue to work with the machine. As soon as the tank is empty, the current cycle is ended, the machine stops and an error message is displayed.
Air Supply
An air supply is required for the micro spray system. The minimum supply pressure is 6 bar.
Clamping Device
The workpiece clamping is designed as a pneumatic two-point clamping for low-burr sections to the left and right of the saw blade. In addition, a manually adjustable vertical hold-down device is attached to the left of the saw blade. Including clamping pressure reduction, each separately adjustable for the main, section and replenishment clamping device. The valves, pressure gauges and the feed controller are located in an easily accessible control panel at the front of the machine.
An air supply is required for the pneumatic clamping system. The minimum supply pressure is 6 bar.
The clamping devices are designed as standard for the use of quickly exchangeable mold jaws.
material replenishment device
The material is replenished via a collet, which is driven by a servo motor and ball screw. The replenishment tension is pneumatic.
The replenishment axis can accelerate up to 0.4g (4000mm/s2).
The preferred length/replenishment length (section length) can be preselected up to a maximum of 9999mm with the positioning control. The single preferred length is 1000mm.
Shortest section length 10mm (shorter lengths on request).
Controlled 0 edge for replenishment facility
Damage (scratches) are avoided as far as possible by pushing on.
For processing crooked profiles; the crookedness must not exceed a maximum value of 1mm/m - deviations must be clarified in individual cases.
Function description:
When pushing in, the material is lifted forwards in front of the 0 edge (fixed surface of the clamping device) and slightly upwards (above the material support). This will
The material is fed in “freely” without touching the clamping jaws.
In return, the rear clamping jaw of the replenishment device is positioned backwards (behind the 0 edge) and downwards (below the material support) during the return stroke. This drives
The replenishment device "freely" back without touching the material.
kerf expansion
The standard cutting gap extension moves the material to the left and right of the saw blade after the cut, on the left via the positioning control, on the right via 2 pneumatic cylinders.
suction points
A powerful extraction system is necessary for the trouble-free operation of the sawing machines. The machine comes standard with 4 connecting pieces
designed:
• 1 spigot upwards, diam.160mm
• Connector diam. 100mm: 1 x backwards, 1 x on the base and 1 x on the saw blade guard
Depending on the cutting performance and design, the extraction system must be specified. We would be happy to make you a detailed offer. For this we would have to
Production requirements (profile cross-sections and cycle times) as well as a hall plan are made available in order to be able to determine the correct location of the system.
material disposal
A rigid support plate is built in as standard to the right of the saw blade, on which the sawn parts are pushed out by the following material.
steering
takes place via a programmable logic controller. The PLC has several programs and several sets can be created behind each program. A set consists of
Number of pieces, section length, material compartment (disposal) and sawing parameters. Furthermore, all movements can be run in manual mode. An operating hours counter is also included. A light barrier is integrated into the control circuit to detect the start and end of the material.
Included:
Machine light (LED)
Machine status light, tricolor (red, yellow, green)
Remote maintenance via VPN connection
This makes it possible to carry out a remote diagnosis via VPN connection in the event of any faults on the sawing machine.
The sawing machine is designed for a voltage network of 400V/50Hz (3LNPE 400V/50HZ).
2 additional machine equipment
Additional vertical clamping device
To the left of the saw blade, eliminating the need for manually adjustable vertical hold down
Additional pneumatic clamping device
on the vertical tension yoke above the replenishment device
blow-out device
In order to keep the clamping area of the main and section clamping between the movable clamping jaws and the material as chip-free as possible.
3 feeder
Use without loading magazine
In conjunction with a feed roller conveyor, the material can be fed into the machine by hand. The replenishment device recognizes the beginning of the material via a light barrier and takes over the bar and automatically positions it in the cut position. From then on, the inserted bar is sawed open in automatic mode until the next bar is loaded by hand.
backstop
Manual reloading and automatic pick-up of the profile bars without opening and closing the protective hood, consisting of a bracket with a pneumatically controlled backstop.
Infeed roller conveyors for the EISELEVMS series
(Roller conveyor width 420mm, roller width 407mm) in SPECIAL DESIGN
• Support height 900mm
• Ball-bearing, robust steel rollers
• Attachment on the left
• with insert sheets
• Including cross braces, as it is free-standing next to the machine with 4 template polders, each 800mm deep + plastic pad
disposal facilities
Discharge roller conveyors, with 407 mm roller width, plastic rollers
Total length 4000mm
livery
RAL7035 light grey
suction system
ALKO Power Unit 250P
The design of the machine and system corresponds to the EC Machinery Directive 2006/42/EC and the applied, harmonized European regulations and standards.
Specifications
Manufacturer | BEHRINGER EISELE |
Model | VA-L350NC2 |
Year | 2017 |
Condition | Used |